Инженерное значение колодезных конструкций сохраняет актуальность в современном строительстве, несмотря на многовековую эволюцию технологий. Вертикальные коммуникации различного назначения — водонапорные системы, канализационные магистрали, смотровые шахты — формируют базовую инфраструктуру как в масштабных градостроительных проектах, так и в загородном строительстве.
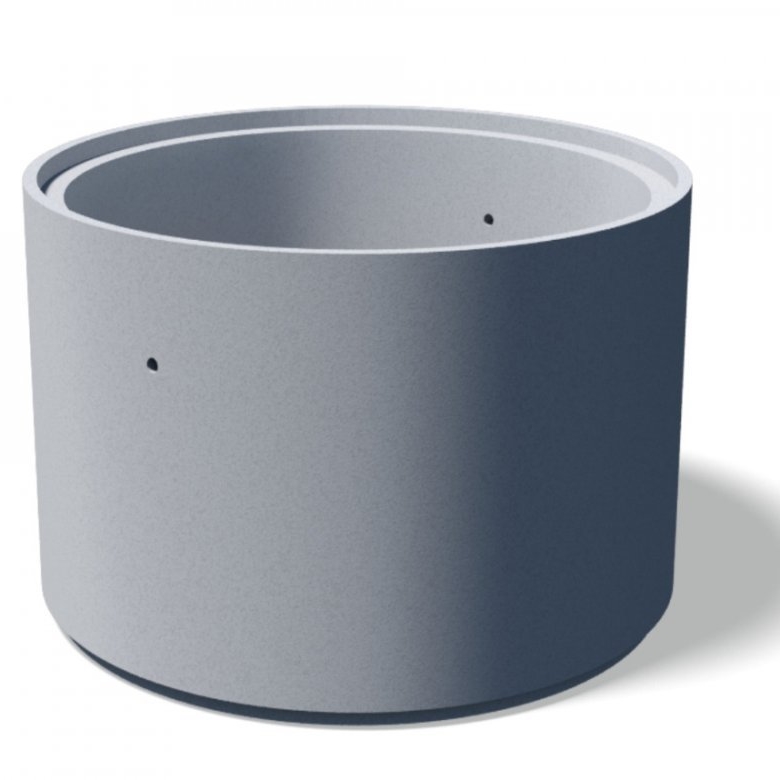
Материаловедческие аспекты и конструктивные особенности
Железобетонные кольца демонстрируют оптимальное соотношение технологических параметров при возведении вертикальных шахтных сооружений. Армированный бетон, выступающий основным конструкционным материалом, обеспечивает исключительные прочностные характеристики и продолжительный эксплуатационный период. Альтернативные изделия из поливинилхлорида, характеризующиеся пониженной массой и стоимостью, существенно уступают по показателям долговечности.
Конструктивное исполнение железобетонного кольца представляет интеграцию несущего армированного каркаса и высококачественного товарного бетона. Специализированные добавки в составе бетонной смеси формируют комплекс эксплуатационных характеристик, определяющих функциональное назначение изделия.
Типологическая классификация колодезных колец:
- Опорные конструкции: обеспечивают структурную основу для монтажа и надежной фиксации люков;
- Стеновые элементы: предназначены для последовательного монтажа и формирования вертикального ствола шахты;
- Доборные изделия: характеризуются нестандартными габаритными размерами для достижения проектной глубины;
- Замковые конструкции: интегрируют специальные механизмы фиксации для применения в зонах геологической нестабильности;
- Конструкции с интегрированным днищем: повышают статическую устойчивость и конструкционную прочность;
- Регулировочные элементы: обеспечивают возможность увеличения глубины желоба до 500 мм.
Параметрическая стандартизация
Размерные характеристики колодезных колец регламентированы государственными стандартами. Диапазон внутренних диаметров охватывает значения от 700 до 2000 мм. Высотные параметры варьируются от 100 до 1000 мм с унифицированным шагом 500 мм. Железобетонные конструкции изготавливаются в диапазоне высот 700–1200 мм. Проектные решения учитывают превышение внешнего диаметра над внутренним.
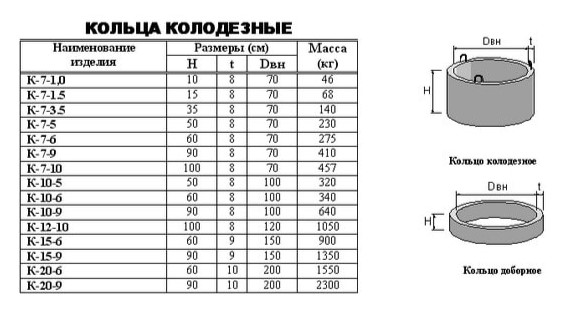
Геометрическая конфигурация
Базовая геометрическая форма колодезных колец представлена правильным цилиндром. Опорные конструкции с увеличенным внешним диаметром характеризуются асимметричным позиционированием люка, что обеспечивает эргономичность при техническом обслуживании магистральных коммуникаций.
Система идентификации
ГОСТ 23009 регламентирует цифробуквенную систему маркировки. Числовой компонент указывает внутренний диаметр в дециметрах и высоту изделия. Буквенные индексы определяют функциональное назначение:
- КВГ: элементы газопроводных и водопроводных систем;
- КФК: компоненты канализационных и водопроводных коммуникаций;
- КЛК: конструкции водосточных систем;
- КДК: элементы внутриквартальных коммуникаций;
- КО: опорные конструктивные элементы;
- КС: стеновые компоненты.
Дополнительную номенклатуру составляют плиты перекрытия (маркировка ПП, ПК), плиты днища (ПН, ПД) и железобетонные стаканы.
Производственная технология
Технологический процесс производства регламентируется ГОСТ 8020-90. Применяются бетонные композиции марок М200–М500 с учетом климатических условий эксплуатации. Армирование осуществляется проволокой диаметром 0,6–10 мм в зависимости от габаритных параметров изделия.
Производственный цикл базируется на использовании шаблонов — пустотелых цилиндрических форм, оснащенных вибрационными механизмами для обеспечения гомогенности бетонной массы. Армирование большого диаметра применяется исключительно для формирования монтажных петель.
Нормативная документация регламентирует использование следующих материалов:
- Арматурная проволока Вр-I (ГОСТ 6727);
- Горячекатаная стержневая сталь классов АI–А-III (ГОСТ 5781);
- Термически упрочненная стержневая арматура Ат-IIIС и Ат-IVС (ГОСТ 10884).
Эксплуатационные преимущества
Модульная архитектура железобетонных колец обеспечивает комплекс технических преимуществ:
- Длительный эксплуатационный период: базовый срок службы составляет 50 лет с потенциалом увеличения до 70–80 лет;
- Технологичность монтажа: процедура установки не требует специализированной квалификации персонала;
- Экономическая эффективность: оптимальное соотношение стоимостных параметров позволяет реализовывать проекты в рамках минимальных бюджетных ограничений;
- Комплексная устойчивость: изделия демонстрируют высокие показатели морозостойкости, водонепроницаемости, пожаростойкости при сохранении конструкционной прочности.